Maximizing Slot Fill for High-Performance Electric Motors
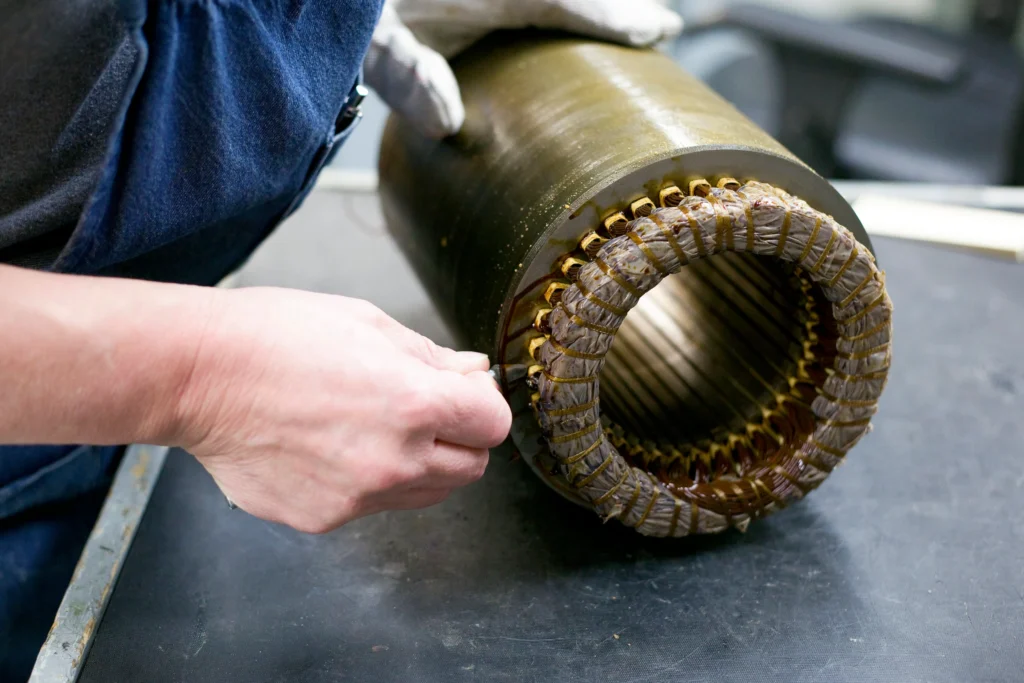
When designing electric motors, particularly for high-performance applications such as aerospace, defense, and advanced mobility, every detail matters. One critical factor that determines the motor’s performance is slot fill—the percentage of space within a stator slot that is filled with conductive materials like copper wire. High slot fill is essential for increasing torque output, efficiency, and overall power density, making it a key parameter in the design and manufacturing of custom motors. However, maximizing slot fill also introduces several manufacturing challenges and trade-offs that engineers must carefully navigate.
In this blog, we will explore the concept of slot fill, the importance of optimizing it for high-performance motors, the associated design considerations, and the challenges of achieving high slot fill in real-world applications.
What is Slot Fill?
Slot fill refers to the ratio of the cross-sectional area occupied by copper wire inside the stator slot to the total available space in the bare slot. In an ideal world, 100% slot fill would yield the maximum possible output torque for a motor, as more copper means more current and thus more torque. However, achieving 100% slot fill is impossible due to several practical constraints, including insulation, slot liners, wedges, and the inherent gaps created by the round shape of the wire​.
In typical applications, copper wire accounts for around 65% of the slot fill, with the remaining space taken up by insulation, air gaps, and other materials​. Higher slot fill factors are desirable, particularly in applications where power density is critical. However, as the slot fill percentage increases, so do the manufacturing complexity, cost, and the risk of quality issues​.
Why High Slot Fill Matters
- Increased Torque and Power Density
The more copper that can be packed into a stator slot, the more current it can carry, leading to higher torque output. This is particularly important in high-performance applications where space is limited but power demands are high. Aerospace, defense, and advanced air mobility industries often require motors with high torque density to ensure efficiency and reliability in critical operations​​. - Improved Efficiency
Higher slot fill reduces the electrical resistance within the motor’s windings, which in turn reduces energy losses due to heat. Motors with higher slot fill tend to be more efficient, meaning they can convert more electrical energy into mechanical energy, which is crucial in industries where energy efficiency directly affects operational costs and performance​​. - Optimized Thermal Management
The more copper used in the windings, the better the motor can dissipate heat, provided other factors like insulation and materials are carefully selected. High slot fill can help maintain optimal operating temperatures, improving the motor’s durability and extending its lifespan​.
Design and Manufacturing Challenges
Achieving high slot fill is a complex task that requires careful attention to both design and manufacturing processes. Some of the key challenges include:
- Insulation and Material Considerations
As the slot fill percentage increases, space for insulation decreases. Engineers must select insulation materials that are thin yet durable enough to withstand the mechanical and thermal stresses of high-performance applications. Common insulation materials include Nomex, Kapton, and powder coatings, each with unique thickness and thermal properties that must be accounted for in the design​​. - Wire Shape and Arrangement
Round copper wires, typically used in motor windings, create unavoidable air gaps between the strands, reducing the potential slot fill. To mitigate this, some designs use precision-wound coils, where the wire is tightly packed in a defined pattern to maximize space usage. However, this adds complexity to the manufacturing process​.
In some cases, engineers may opt for rectangular or square wires instead of round wires. These wires fit together more efficiently, reducing the gaps between them and allowing for higher slot fill percentages. However, these wires are harder to work with and may require custom tooling​​. - Aspect Ratio and Slot Design
The aspect ratio, or the relationship between the stator’s length and its diameter, directly affects the maximum achievable slot fill. Higher aspect ratios make it more challenging to insert wires into the slots, particularly toward the middle of the stator stack. This is because it becomes harder to apply the necessary pressure to compact the wires without damaging them​​.
In addition to aspect ratio, the shape of the stator slot itself plays a significant role in slot fill. Slots with rounded corners, for example, can accommodate more wire compared to sharp-cornered slots, where insulation and wire cannot perfectly conform to the shape​​.
Advanced Manufacturing Techniques
To achieve high slot fill percentages, particularly in applications where power density is critical, advanced manufacturing techniques are often employed:
- Compression Winding
In this method, wires are compressed during the winding process to pack them more tightly into the slot. Compression winding can significantly increase slot fill but requires specialized tooling and precise control to avoid damaging the wire insulation​. - Segmented Stator Construction
Segmented stators allow engineers to wind coils around individual stator teeth before assembling them into the full stator stack. This eliminates the need to thread wires through the narrow slots of an already-assembled stator, which can be a significant bottleneck in the manufacturing process. Segmenting the stator can lead to much higher slot fills, but it adds complexity to the assembly process​​. - Precision Winding
Precision winding techniques involve placing each wire strand in a predetermined position within the slot, minimizing air gaps and maximizing copper fill. This process can be done manually or with highly specialized machinery. While precision winding offers the highest possible slot fill, it is labor-intensive and time-consuming​​.
Balancing Performance and Manufacturability
One of the key trade-offs when pursuing higher slot fill is between performance and manufacturability. While higher slot fill improves torque density and efficiency, it also increases the complexity of the manufacturing process, driving up costs and potentially leading to quality issues if not done correctly​​.
For motors used in mass production, where cost and speed of manufacturing are critical, a slot fill of 60–70% is typical. However, for custom motors used in high-performance applications, where performance is prioritized over cost, slot fill percentages of 80% or more may be achievable through advanced techniques like compression winding and segmented stator construction​​.
Conclusion
Achieving high slot fill is a critical factor in the design of high-performance electric motors, particularly in industries where power density, efficiency, and reliability are paramount. While there are significant challenges in reaching high slot fill percentages, advanced manufacturing techniques and careful material selection can make it possible. For custom motor applications, such as those designed by Windings Inc., maximizing slot fill is an essential part of delivering motors that meet the stringent requirements of aerospace, defense, and advanced mobility​​.
By balancing the need for high performance with the realities of manufacturability, engineers can push the boundaries of what is possible in electric motor design, delivering solutions that meet the ever-increasing demands of modern industries.
For more information on how Windings can help you with your motor design and manufacturing needs, visit Windings Inc. or contact our team of experts directly.